Development History of TASU Industrial Rubber Injection Technology
2015
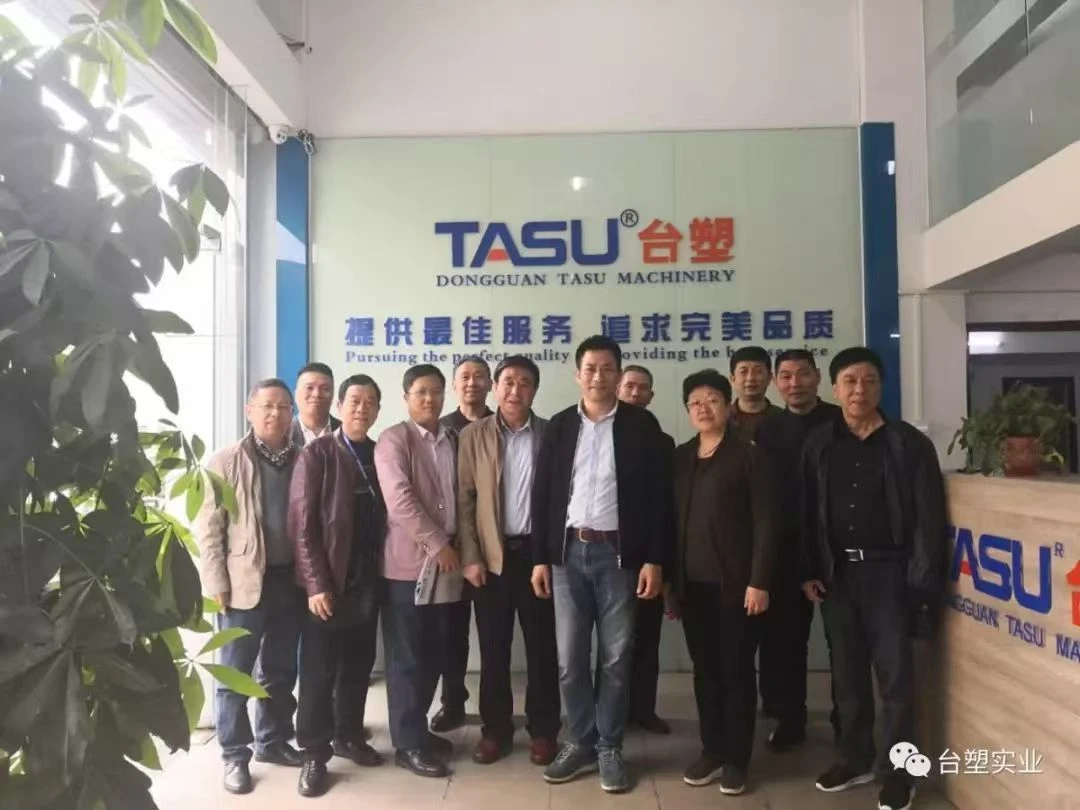
First Generation Equipment
• Features: Focusing on the injection of rubber modified material particles, the development of basic rubber injection machines was realized for the first time.
• Challenges: Faced with the insufficient wear resistance and tear resistance of modified materials, as well as the complexity of the process, the market adaptability is poor and the overall effect is not good.
2016

Second Generation Equipment
• Features: Improve the shortcomings of the first generation, introduce pelletizing technology, and cut the rubber into pellets for injection.
• Breakthrough: Use traditional hot runners to improve the flow channel design and preliminarily solve the problems of material fluidity and molding efficiency.
• Limitations: The pelletizing operation is complicated, the pellets are easy to stick together, the hot runner design wastes a lot of materials, and the operation difficulty is still high.
2017
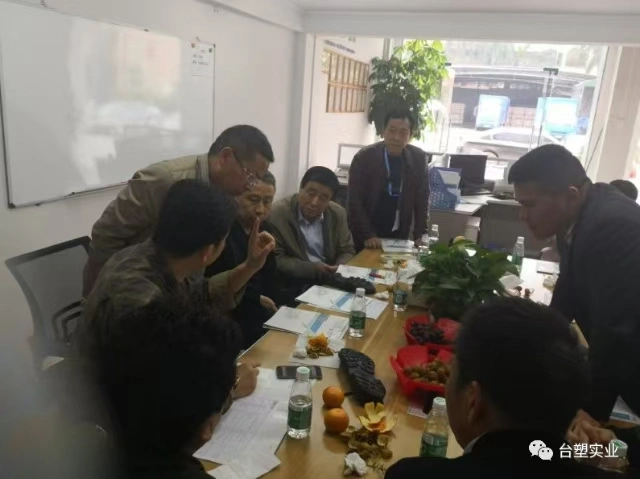
Third Generation Equipment
• Features: In response to the problems of the second generation, the feeding link and screw structure are further improved to achieve smoother injection.
• Breakthrough: Started to try mold improvement, introduced the concept of the cold runner to reduce material waste and accumulate experience for the cold runner technology of the fourth-generation equipment.
• Limitation: The overall efficiency and stability need to be improved.
2018
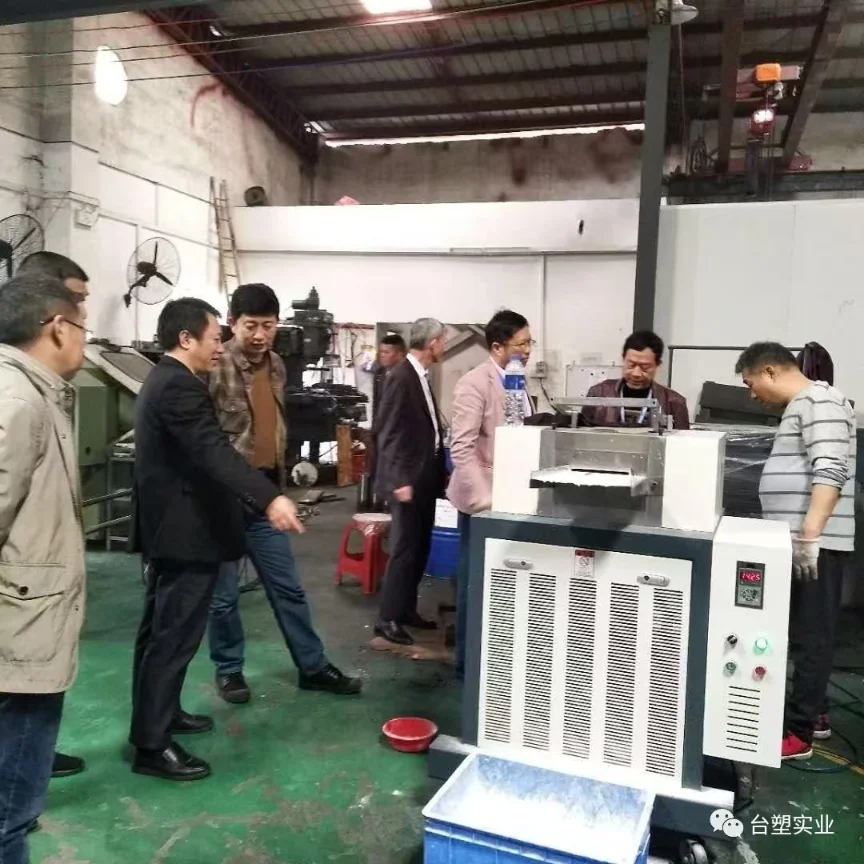
Fourth-generation equipment
• Features:
Officially introduced cold runner design to effectively reduce material waste and operation complexity.
Initially, automated feeding technology was tried to achieve efficient feeding.
• Breakthrough: The cold runner design became the first solution in the industry to integrate cold runners into rubber injection equipment.
2019
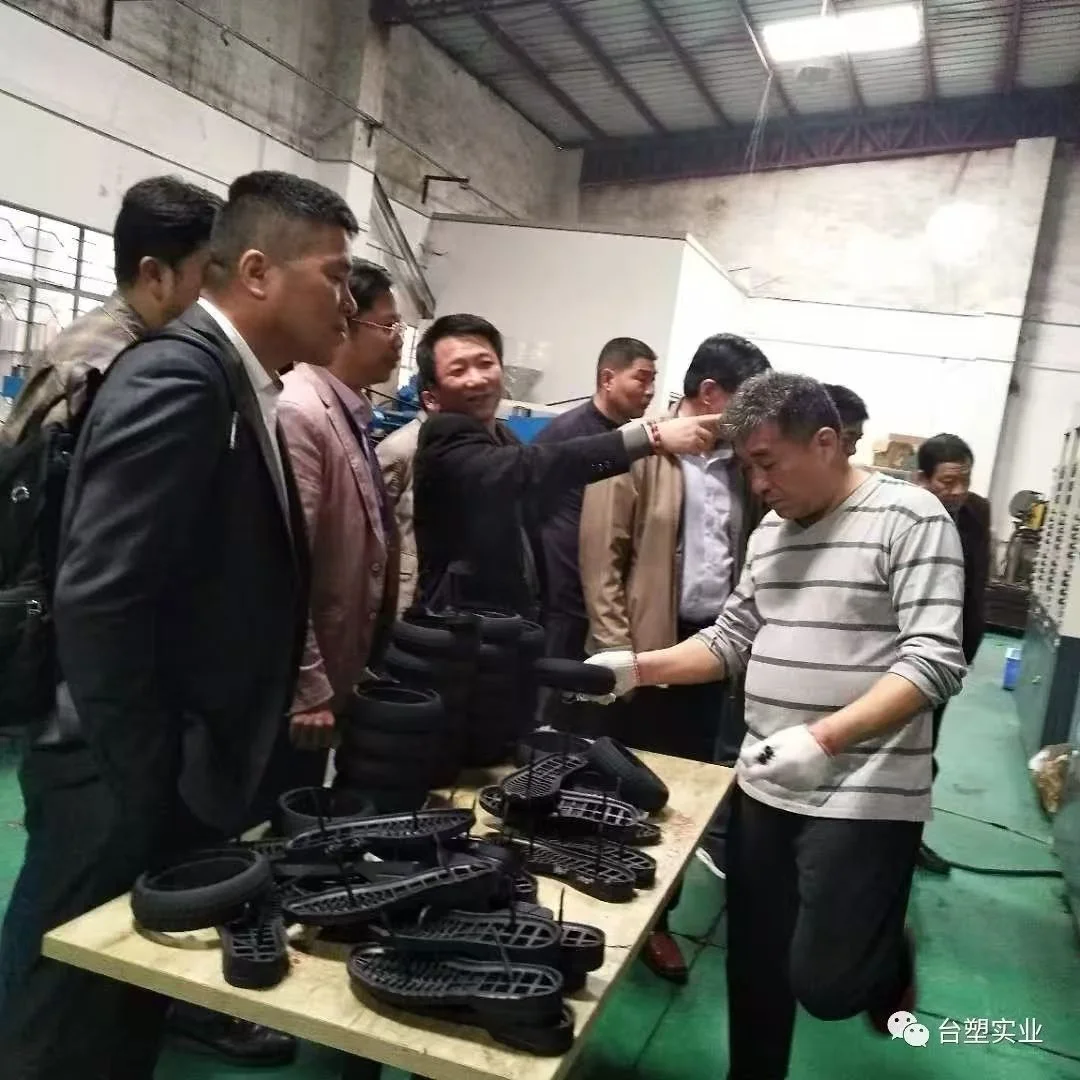
Fifth-generation equipment
• Features:
Feeding monitoring and alarm functions improve the reliability and stability of equipment operation.
Core technology breakthrough: runner plate nozzle manufacturing technology to prevent raw material backflow. By setting up flow channels, limiting protrusions, three-claw blocks, and spherical structures, one-way flow is achieved.
Significantly improve injection accuracy and reduce defective product rate.
• Advantages: Eliminate the backflow of rubber raw materials and improve product quality and production efficiency.
2021
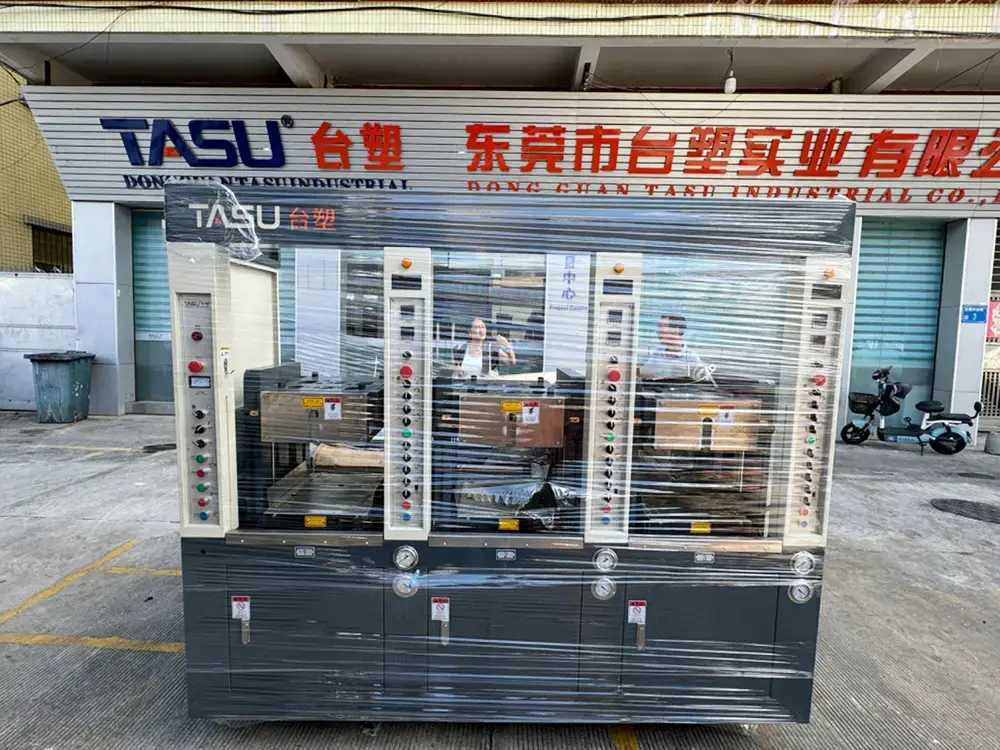
Sixth-generation equipment
• Features:
Optimize cold runner and anti-backflow technology, and the equipment is more stable and reliable.
Increase production according to customer needs while significantly reducing energy consumption.
• Advantages: Lay a solid foundation for large-scale commercial use, and the customer market will gradually accept it.
2024
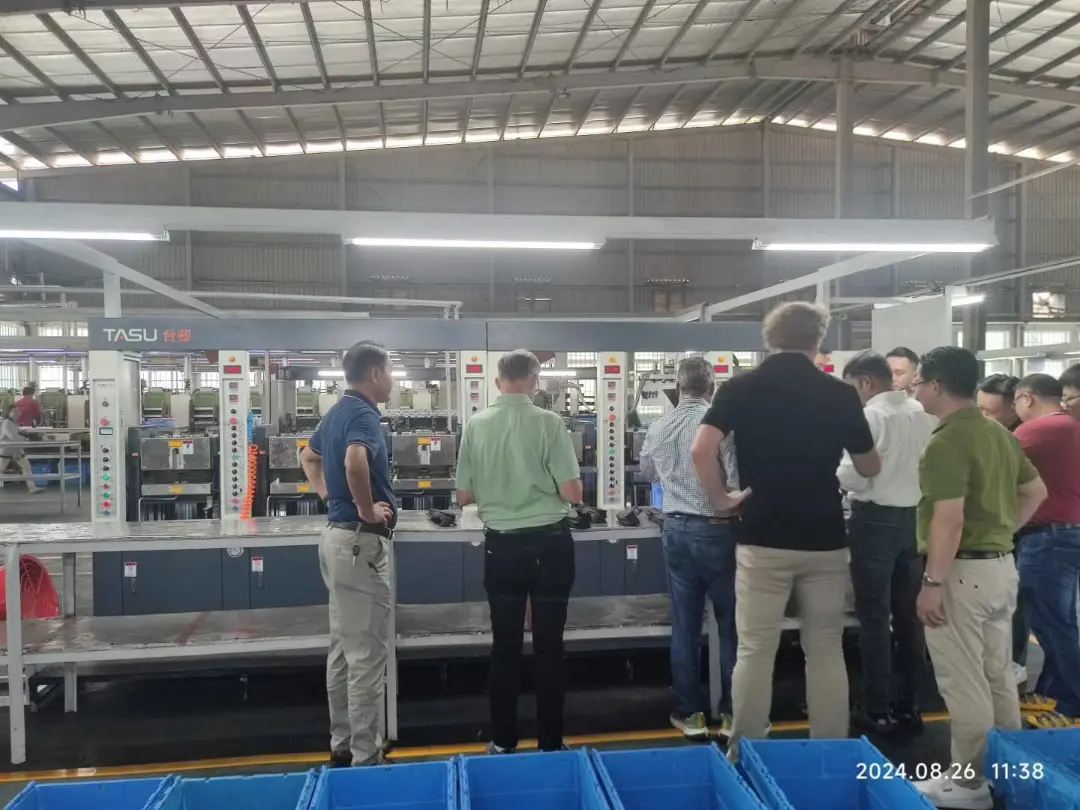
Seventh-generation equipment
• Features:
Adopt a dual servo system to increase production capacity and greatly shorten operation response time.
Enhance the precise control of mold opening stroke, achieve a precision of a few tenths of a millimeter, effectively exhaust, and meet the needs of complex molds.
• Advantages: Combining high precision and high efficiency, it has become a market benchmark equipment.